Induction Heating
Alternating current through induction coil surrounding the part to be treated induces eddy current through the part which is thus heated. The advantage of such heating is that no gas or liquid source for heating is used and coil can be shaped to surround the part geometrically. Figure shows example of induction coils, which normally are made in copper or copper based alloy which are water cooled. The coil is also designed for quenching the part after heating. For surface hardening requiring local heating induction heating is suitable.
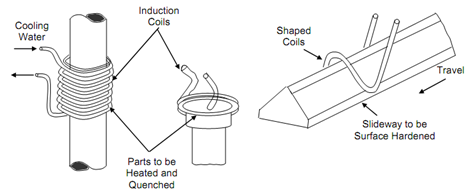
Figure: Coils for Induction Heating
If the heating is not through salt bath, then the job to be treated is subject to varying atmosphere which could be atmospheric air or any one of several gases. Surface oxidation, tarnishing and decarburisation are the problems which the metals face. Oxygen can cause oxidation, rusting and scaling. Carbon dioxide may cause decarburisation depending upon its concentration in furnace atmosphere. Thin blue film, is formed on the surface in the presence of water vapour. Bluing of surface is done for improving surface appearance. Nitrogen provides a neutral atmosphere. Vacuum furnaces often used for small and accurately finished parts provide complete safety from effects of atmosphere.