Aggregate Production Planning Requirements:
The next step is to calculate the cost of each plan. This requires the series of simple calculations as shown in Table3 to 6. Each of these four plans focused on one particular cost, and the first three were simple pure strategies. Clearly, there are several feasible plans, some of which would use combinations of workforce changes, over time and subcontracting. In practice, the ultimate plan chosen would come from searching a variety of alternatives and future projections and beyond the six month planning horizon is utilized.
Keep in mind that the cut-and-try approach does not guarantee discovering the minimum cost solution. However, spreadsheet programs such as Microsoft Excel may perform cut-and-try cost estimates in seconds and have elevated this kind of what-if analysis to a fine art. More sophisticated programs may generate much better solutions without the user having to indicate, as in cut and try method.
Table: Aggregate Production Planning Requirements
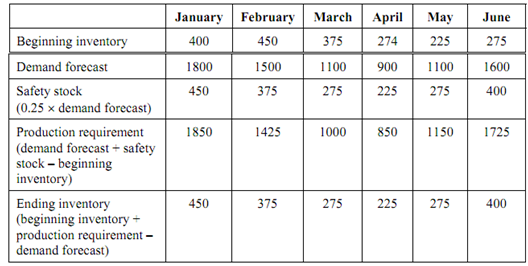