Process Knowledge in the Form of Decision Logic and Data
Basically, the matching of part geometry requirements with the manufacturing capabilities is accomplished in this phase using process knowledge in the form of decision logic and data. All the activities of process planning are performed automatically. Examples include the selection of processes, machine tools, tools, jigs or fixtures, inspection equipment, and sequencing of operations. Setup and machining times are calculated. Operations instruction sheets are generated to help the operators run the machines in case of manual operations. If the machines are numerically controlled, the NC codes are automatically generated.
Manufacturing knowledge is the backbone of process planning. The process of acquisition and documentation of manufacturing knowledge is not a one-time activity but a recurring dynamic phenomenon. Furthermore, the sources of manufacturing knowledge are many and diverse, such as the experience of manufacturing personnel; handbooks; suppliers of major machine tools, tools, jigs or fixtures, materials, and inspection equipment; and customers. To use this wide spectrum of knowledge ranging from qualitative and narrative to quantitative, it is necessary to develop a good knowledge structure to help provide a common denominator for understanding manufacturing information, ensuring its clarity, and providing a framework for future modifications. Tools available for the purpose include flowcharts, decision trees, decision tables, iterative algorithms, pattern recognition techniques, concepts of unit-machined surfaces, and artificial intelligence tools such like expert system shells.
Table 1: Boolean Value-Type Entries
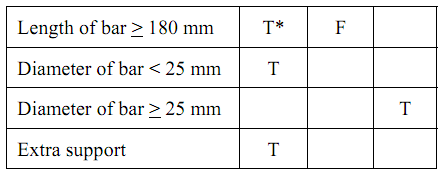
* T : True; F : False; Blank : Do not care.