Tracking Direct Materials
Jack keeps full records of the material released to each job. When Donnie gathered up light bulbs, tape, breakers, wire, and wire nuts on the morning of the 14th, some system required to be in place to "check out" this material. The document which is used for this process is known as the "materials request" or "materials requisition" form. This form will show which material is leaving the available raw materials stock and being put into the production. At times a separate form is prepared for every item, and sometimes a running list similar to the given below is used:
Castle Electric Materials Requisition
Employee: Donnie Odom
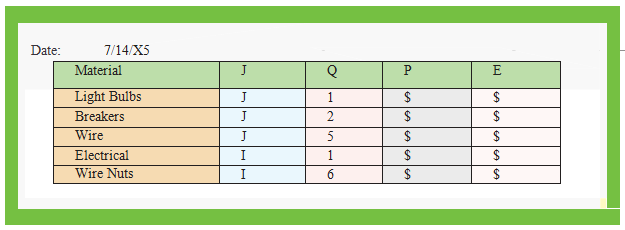
This form gives essential documentation to safeguard and track the inventory; a manager who fails to control and monitor the inventory does so at great peril! It also reveals that "direct material" for the billboard task (Job A) was $150 i.e. the light bulb. The wire nuts and tape might have been used on the billboard will be dealt with as an overhead which is discussed later.
Before moving on to overhead, you are required to know one more thing about the "materials requisition" form; although illustrated form lists material cost, which will not always be the case. At times, a business may not be particularly interested in letting employees to see the cost information, or cost information may not be readily obtainable. In any of the case, the form will instead comprise a part or the serial number. A subsequent clerical task will be to recognize the cost of the particular parts which were put into the production. Great care should always be taken to match right cost to the right item, and in right quantity. For instance, the 500 feet of wire might be on one roll, but it is priced by the foot, and quantity must be 500 feet, not 1 roll; the job cost calculation would be bit incorrect if only $0.14 were assigned to one roll of the wire!