Supplier Quality System
For important purchases, ensuring acceptable supplier quality is critical. Conducting supplier quality audit is one of the steps in making sure the selection of a capable supplier. A supplier quality audit should follow at least the below mentioned steps. The figure below describes the steps in supplier audit.
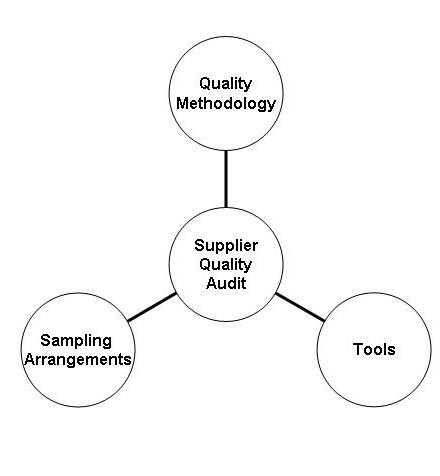
Figure : Supplier Quality Audit
Many quality methodologies are used in today's world including total quality management, six sigma and so on. The audit team verifies the methodology the supplier's employs and how it's being used.
Tools: The auditing team verifies how the supplier monitors the quality of the product. One common used tool used is Statistical Process Charts (SPC). SPC recognises an acceptable range of quality measurements and then graphs actual measurements both between upper and lower limits of acceptability and outside those limits.
Sampling arrangements - The audit team verifies the situation in case of mass production. In case of mass production, each and every unit made is not inspected. The audit questions as to how the supplier chooses the size and composition of inspected samples. Suppliers very frequently use numbers to gauge their quality performance. The supplier is asked to produce reports of few years with the metrics listed. The audit also checks if the supplier inspects the items before shipment. The inspection methodology used must be similar to the way the company actually evaluates conformance.
A purchasing system includes three major activities:
- Specification of requirement.
- Selection of a supplier.
- Supply chain management.
The overall quality objective is to meet the needs of the purchaser with a minimum of incoming inspection or later corrective action, this objective in turn leads to minimising overall cost.
Goals and needs for suppliers must be aligned with those for each link in the supply chain, particularly the end user and the purchasing organisation. These goals and needs consist of quality parameters and general business issues.
For modern products, quality planning begins before a contract is signed. Such planning must recognise two issues:
- A full understanding of the use of the product must be transmitted by the buyer to the supplier.
- A product that meets all fitness-for-use requirements could be provided by the supplier and the information must be obtained by the buyer for sure.
The complexity of many modern products makes it tough to communicate usage needs to a supplier in a specification. Not only are the field usage conditions of a complex product sometimes poorly known, but also the internal environments surrounding a specific component may not be known until the complete product is designed and tested. For example: specifying accurate temperature and vibration requirements to a supplier of an electric component may not be feasible until the complete system is developed. Such cases require, at the least, continuous co operation between supplier and buyer. In special cases, it may be mandatory to award separate development and production contracts to discover how to finalise requirements.
Situations might require two kinds of specifications:
- Specifications defining the product requirements
- Specifications defining the quality related activities expected of the supplier i.e. the supplier's quality system.
Defining required activities within a supplier's plant is sometimes necessary to ensure that a supplier has the expertise to conduct the full program needed for a satisfactory product. For few products, government regulations require that a buyer impose certain processing requirements on suppliers.
In case of complex products for which a supplier is asked to design and manufacture a product, the supplier can be required to include in the proposal a preliminary test plan; or other prediction; a failure mode, effect and criticality analysis; a reliability test plan or other reliability analyses.