Introduction:
The scheduling system that is followed by the maintenance department is not well established and is dependable on employee's personal judgment. There were a lot of flaws found in the system that could self-cannibalize and lead to severe consequences in the near future. The purpose of this project is to establish a standard scheduling system, using the appropriate scientific tools, to be used everywhere and every time.
Recognizing the need:
As mentioned in the previous sections in this report, the maintenance department is busy helping the emergency department for almost five months a year. This, clearly, leaves little time for the department to achieve its year-long plan. The department gets overwhelmed two months before the end of each year; this is because the amount of work that is remained usually exceeds the resources needed to cover it. This leads management to extend working hours and compensate workers for extra hours worked.
Every year, the department gets busier than the previous year. This goes to the fact that the company installs more substations into the city in order to satisfy the enormous expansion in Riyadh's metropolitan area. Enough said, the resources in hand cannot satisfy the huge demand, and the department needs a new and more stable way to schedule its preventive maintenance processes.
Defining the Problem:
For a better understanding of the situation, I'll give a brief overview of the technical part of the process. There are two different types of power stations in which the department deals with, primary stations and substations. The primary station, as the name suggests, delivers and distributes power to many substations that in return deliver power to consumers. Each substation is powered by two primary stations, so in order to perform maintenance; the substation has to be isolated from both ends.
After the yearly plan has been listed by the concerned director, each area manager gets a list of all substations that require preventive maintenance in that specific year. Using excel, each substation is categorized by the number of consecutive adjacent substations, powered by the same primary substations, which also need preventive maintenance. Then, the substation falls in a program named after the number of substations. For example, if substation S1 is adjacent to five other substations and all are powered by the same primary stations, then S1 falls under "Program 6".
After this is done to all substations, the planner starts making the monthly schedule for the whole year starting with the largest programs first, and ending with the smallest (most probably one-sized programs). When the monthly schedule is constructed, the planner makes the weekly schedule at the end of each month. Then, the planner makes the daily schedule at the end of each working day to avoid delay (figure 2).
I was assigned to join the northern area of Riyadh because it has the lowest density of substations, and is relatively the easiest area to work in. One of my duties was to help in the distribution of maintenance teams into the field. There are three types of field maintenance workers:
1. Maintenance Technician: capable of performing all substation maintenance tasks, i.e. changing oil.
2. Crew Chief: Responsible of supervising 3-5 maintenance technicians.
3. Senior Operator: Possesses most field experience of all, is responsible of power isolation process, communicating with control engineers in the office, and coordinating with the involved senior operators.
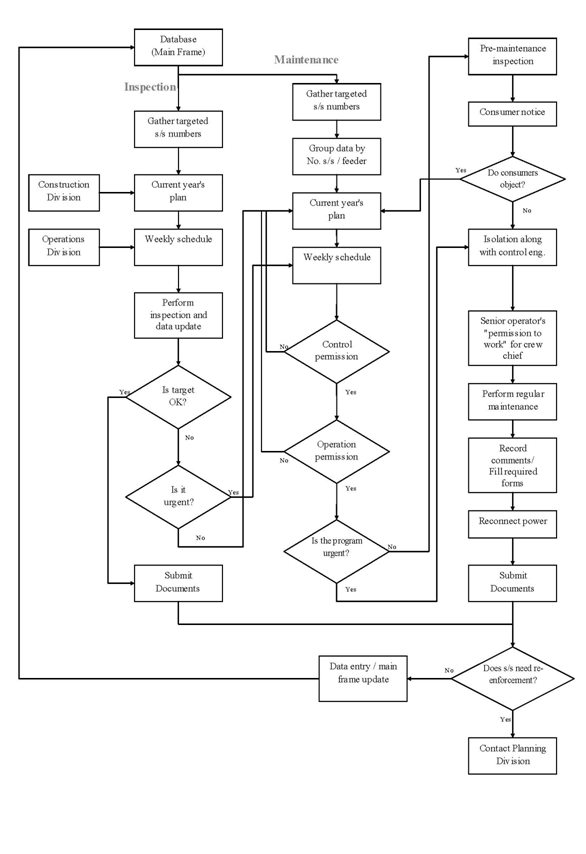
Northern Riyadh's office has 6 teams (6 crew chiefs and 24 technicians) and 3 senior operators. When performing preventive maintenance, all the concerned substations must be isolated. Isolation process is done in the primary stations, and must be done by a senior operator with the help of a control engineer. After isolation, senior operator gives permission to the crew chief of each maintenance team to start the work. All teams perform maintenance work on the substations simultaneously. After that, crew chiefs report back to the senior operator and inform him that the work is completed so he can connect the power back on.
When making the monthly schedule, the planner chooses the largest programs because they allow all teams to work simultaneously, which results in more utilization of workers. However, when the large programs are done with, the remaining small programs left cause disturbance to the planner and the workers. They require as many senior operators as all the other programs but only few teams, which would leave rest of the technicians idle for that time. Moreover, they would force one senior operator to work double the regular load his fellow colleagues are working. Other problems would arise, such as delay, misutilization of workforce, and additional cost for extra time compensation.
Planning the Tasks:
In order to design an appropriate model, certain tasks have to take place in a certain order. A list of tasks is as follows:
1. Comprehend the process in theory.
2. Visit the field for closer and practical look.
3. Study past schedules.
4. Define alternative approaches.
5. Evaluate alternative approaches.
6. Select alternative.
7. Test and compare output to historical schedules.