Static Unbalance:
This arises when two EQUAL unbalance masses are positioned at opposite ends of a rotor and spaced at 180 from each other. If placed on knife-edges, the rotor would be statically balanced. However, when the rotor is rotated, the out of balance masses will cause a centrifugal force to act at each end and hence each end will vibrate independently as shown in figure.
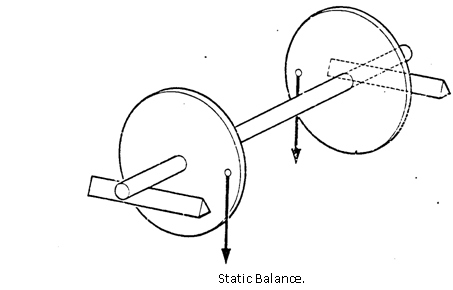
Dynamic Unbalance
This occurs when the unbalanced masses may be either unequal in size or positioned at some angle other than 180 to each other, or even both of these conditions. These unbalanced forces now cause the rotor to vibrate.
FAN BALANCING
Before we look at fan balancing we must first look at vibration analysis techniques adopted on modern gas turbines and the reason for doing it. One of the requirements of an on-condition maintenance policy is that defects can be detected sufficiently early to permit rectification before secondary damage occurs. The analysis of engine vibration signatures is becoming an increasingly important tool for detecting early failure in mechanical components.
A vibration monitoring system begins with a sensor, which may be a velocity transducer or a peizo electric accelerometer. They both convert the mechanical vibration of the machine into an electrical signal proportional to the vibrations produced and together with the associated electrical circuitry feed signals to either cockpit mounted gauges warning systems or a separate vibration analyser.
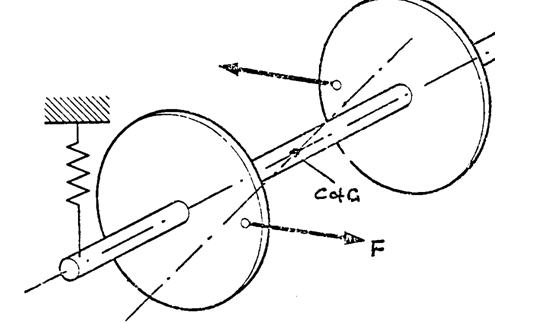
Velocity Transducer
This device operates on the principle of a permanent magnet to move within a coil, inducing voltage. Because of the moving parts with all the inherent disadvantages of wear, friction, etc. they have been superseded by the peizo electric principle.
Peizo Electric Accelerometer
In this device, vibrating forces are transmitted to a peizo electric disc the resultant deformation of the disc produces an electrical charge. Accelerometers have a greater frequency range than velocity transducers and their lack of moving parts makes them a much more stable and reliable means of collecting the basic vibration signal.
Many different specifications for accelerometers and transducers are available and some of the considerations which govern their choice are:-
(1) DYNAMIC RANGE. The amplitude range over which the device is required to perform.
(2) SENSITIVITY. The severity of the vibration liable to be encountered.
(3) FREQUENCY RESPONSE. The full operating frequency range required.
(4) TEMPERATURE RANGE. The upper and lower temperature extremities to which the device will be subjected and also any heat soak conditions.