Production of Chemicals from Coal
Coal has been considered a major component of U.S. energy reserves for a long time, and more recently it has become an important raw material for the production of chemicals. The worldwide abundance of coal, as reflected in Table, and its proximity to sites where it can be used, have made it an attractive alternative to more costly or less strategically located feedstock. Most approaches to the conversion of coal to chemicals involve either coal gasification or coal liquefaction, processes that convert solid coal to fluids. The fluids are more easily handled and processed than the original coal; they can be used as fuels site or after pipeline transmission, or they can be converted to chemical intermediates. A secondary but important aspect of these conversion processes is that potentially harmful materials in coal are more easily separated from the fluids produced by gasification or liquefaction than from either the solid coal or the off-gases from its combustion.
The most common coal gasification process involves the reaction of carbon, the primary constituent of coal, with steam to produce carbon monoxide and hydrogen.
C + H2O → Co + H2 (1)
The carbon monoxide and hydrogen can be separated from the other compounds exiting the gasifier and used either as a fuel or a feedstock to a chemical manufacturing process. Simultaneously, oxygen fed to the reactor along with steam reacts with carbon to form carbon dioxide.
C+O2 → CO2 (2)
In addition, there is significant reaction between water and carbon monoxide in the gasifier via the water-gas shift reaction.
CO+H2O ↔ CO2 + H2 (3)
Although Reactions 1, 2 and 3 are the primary reactions in coal gasification, there are important secondary reactions. For example, the hydrogen-rich atmosphere in the gasification reactor causes the formation of hydrogen sulfide from the sulfur usually found in coal and of small amounts of methane.
S + H2 → H2S
C + 2H2 → CH4
Table: Distribution of Proven Coal Reserves In Billions of Tons
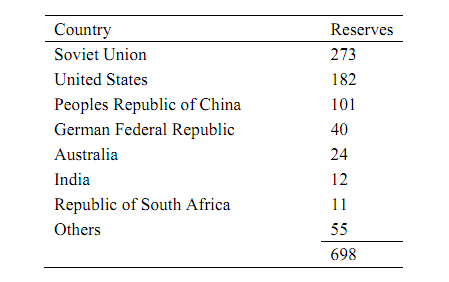
Various hydrocarbon feedstocks other than coal can be used for production of chemicals, including crude oil, natural gas, and wood. Each of these raw materials yields a synthesis gas containing carbon monoxide and hydrogen, much as described above. As the hydrogen-to-carbon ratio in the synthesis gas differs from one feedstock to another, the differences may be used in selecting a feedstock to produce a specific product. For example, natural gas reforming yields a synthesis gas with a high hydrogen content that can be used as a raw material for manufacturing hydrogen-rich products such as ammonia. Gasification of coal, on the other hand, provides a gas with a high carbon monoxide content that can be used as a raw material for producing species with lower hydrogen contents such as acetic anhydride(C4H6O3). The most efficient use of raw material is generally achieved when a feedstock contains hydrogen and carbon monoxide in roughly the proportions required to form the desired chemical product. Of course, there are other factors to consider in choosing a feedstock, such as the projected stability in price and supply of the feedstock and the location of the feedstock in relation to the plant. Your company has plans to build a plant to convert coal to acetic anhydride, a chemical vital to the company's product line. The plant is to produce 160,000 metric tons of acetic anhydride per year. It is anticipated that the completed process will operate continuously 350 days/ yr. The composition of coal from the nearest deposit is given in Table 2. Judging from the sulfur content, production of significant quantities of H2S is expected. Since H2S poisons (deactivates) catalysts used in the conversion of hydrogen and carbon monoxide into acetic anhydride, it must be removed from the gas leaving the gasifier. It is your responsibility to assist with the setting of design variables necessary for sizing equipment.