Process Selection and Process Design
Having identified alternative process sequences and process span choices, the question then to be answered is which of the configurations should be selected for implementation. The answer to this question may not be straightforward. The simplest case would be where, for all of the process sequences being considered, the various processes entailed are already owned by the company, and there is enough free capacity to meet the forecast demand.
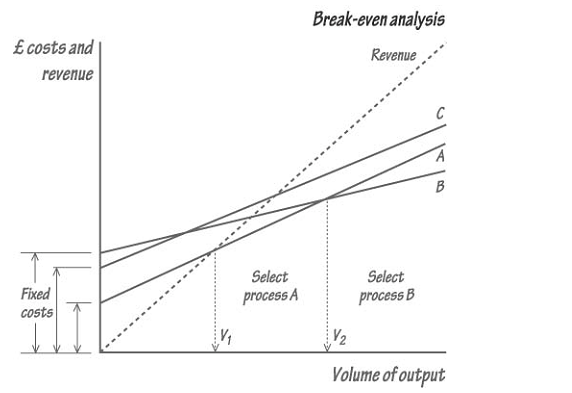
In this case a simple break-even analysis may help in making the choice. For each of the process sequences to be compared, the fixed and variable costs are determined: the fixed costs are those, such as special tooling costs, which are required to set up the processes and are independent of the volume of output; variable costs are those, such as direct labour and material costs, which vary in direct proportion to the output volume. This figure shows, graphically, how the total costs of three process sequences (A, B and C) change with volume of output, alongside the associated revenue. This shows that, for quantities below V1, none of the process sequences recover their costs; for quantities between V1 and V2, process sequence A is the most economical; for quantities greater than V2, process B becomes the least costly. Notice that, in this illustrative example, process sequence C is uncompetitive at all levels of output.
The question may be more difficult to answer if one or more of the competing process sequences require significant capital expenditure. In this case, in addition to break-even analysis, investment appraisal tests may be applied. For example, a process sequence which is attractive according to break-even analysis may be rejected on the basis that its payback period renders the necessary investment too risky. Further consideration of break-even analysis and investment appraisal techniques are beyond the scope of this unit, but are covered at length in Finance and Financial Management.