METHODS OF COSTING:
1. Job costing: Job costing is the essential costing technique appropriate to those industries somewhere the work consist of separate contracts, or batches, each of which is approved by a precise contract or order.
2.Contract costing: It is the type of exact order costing, usually related where work is agree to customer's particular requirements and every order is of extended period for example a building construction etc.
3. Batch costing: It is that type of exact order costing which applies where related articles are manufactured in batches either for sale or for make use of within the undertaking.
4. Process costing: This technique of costing is appropriate where goods or services result from a series of continuous or repetitive operations or processes and products are the same and cannot be isolated.
5. Operation costing: It defines to those techniques where every operation in every stage of production or process is individually planned. After that the cost of over unit is determined.
6. Unit costing/ (Output costing / Single costing): This method is used when the production is consistent and the same and a single article is formed. The entire production cost is divided by the number of units used to get unit or output cost Example: mining, breweries etc.
7. Operating costing: This technique is employed where expenses are incurred for providing services like those rendered by electricity cost ,transport cost, etc.
8. Departmental costing: This defines the technique of ascertaining the cost of operating a cost or department centre. total cost of every department is as- curtained and divided by entire units produced in that department to arrive at unit cost.
9. Composite costing /Multiple: in this technique, the cost of different parts of production is combined after discovering the cost of every and each part manufactured. This technique is appropriate to companies where a product consists of of many assembled parts.
SPECIMEN OF A COST SHEET
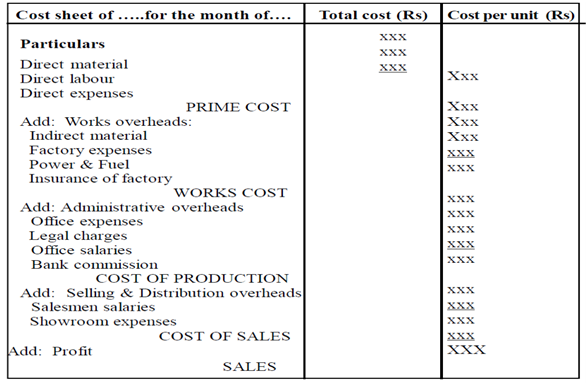