Materials Requirements Calculations - MRP System
MRP is a computer-based 'engine' which carries out calculations in order to determine:
- What is needed, and
- When it is needed.
There are two steps in the process of calculating materials requirements. The first step is to identify the release and due dates, clarify with the customer the due date and then backward schedule by offsetting each item in order to determine the necessary release date.
The next phase is to connect the inventory information. First, look at the basic information flows. MRP explodes inputs taking into account the inventory status and sequence of construction of the products and determines the necessary quantities and timing of orders needed to satisfy the planned completions (master production schedule). This is shown diagrammatically in the figure above.
A simple master schedule is shown below.
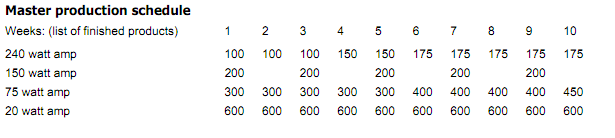
In the figure above, it can be seen that the front-end activity is master production scheduling. The master production schedule drives the MRP and CRP process. The master production schedule is a statement of what the company will produce - it is not a forecast (see the simple master production schedule table). It forms the production plan for the organisation. Creating this plan is a detailed activity for most companies and is achieved by consultation between the departments of marketing, production and financial management.
This means that a computerised MIS will have taken the customers' order and automatically scheduled the plant, including manufacturing and vendors, and be able to supply and deliver his/her special order within a two week period. Henry Ford may have produced for stock, ie 'any colour you wish as long as it's black'.
However, in 1922 it took only four days to turn sheet metal into a Model 'A' Ford.