Line Balancing of Product Layouts
A major consideration in the design of product layouts is that of bottlenecks; just as the strength of a chain is determined by its weakest link, so the output of a production line is limited by its slowest process. The cycle time of the process line shown in this figure is two minutes, determined by the slowest process, 'D'. In this situation, perhaps the first question to address is that of capacity. Assuming an 8-hour working day, the maximum output from this line would be 240 per day (8 hours × 60/2 parts per hour). Therefore, provided anticipated demand does not exceed 240 per day, there should be enough capacity. On the other hand, if the expected daily demand is substantially greater than 240, the capacity might be increased by duplicating process 'D', and using one of the configurations shown in this next figure.
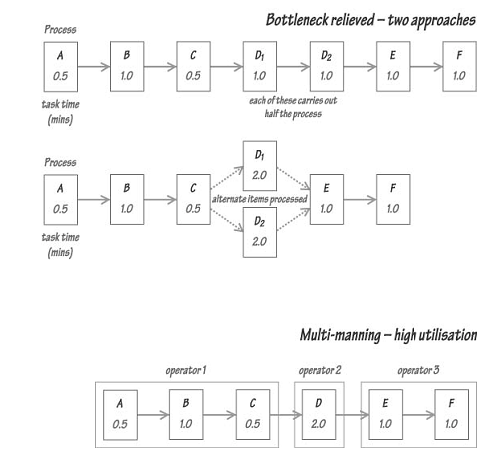
Returning to the process of the figure above, 'Bottle-neck at station D', there is another important issue - utilisation. If this line were to be manned on the basis of one operator per process, then, apart from the operator of process 'D', the labour utilisation would be low. In this simple case, an obvious consideration would be the possibility of multi- manning, as shown in the next figure, where only three operators are required. However, real cases are seldom as simple as this, and it may be advantageous to use a technique devised for the purpose, line balancing, which we will illustrate by means of a slightly more complex example. A company provides a mail-shot service to its clients, and a recently arranged contract calls for 8,000 mail-shots per week to be processed. The mail preparation processes, their precedence relationships and estimated times (including fatigue and personal allowances) are presented in the following table. The company operates an 8-hour day, 5 days per week.