Illustrate theories in planning a machining sequence
A component requires several machining operations to bring it to a final shape. The sequence of these operations are arranged optimally to attain maximum possible production. The following condensed example is presented in order to illustrate basic theories and reasoning followed by process engineer in planning a machining sequence. This example does not consider auxiliary and supporting operations; rather only the major process operations.
The operation sequence for the given pinion blank shown in Figure 11 is given below.
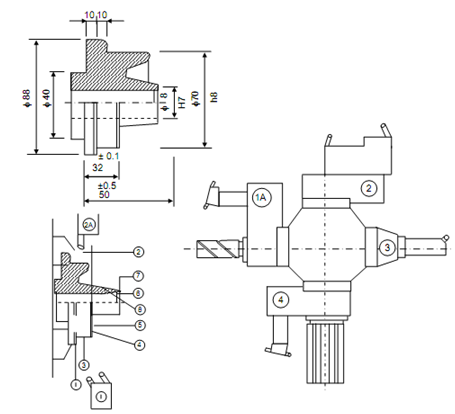
Figure 11: Pinion Blank
Facing of the surfaces 4 and 7 must be done first using two carbide tipped facing tools fixed on front slide of the turret lathe. The process may take 175 seconds per piece for full cycle of operation.
Operation 02
This operation can be done simultaneously with operation 5 by using a combination of tools like bore, drill φ17 HSS and carbide turning tool fixed in position 1 A of square turret. The operations included are
(a) Rough boring,
(b) Semi-finish turning of diameter 3, and
(c) Semi-finish facing of face 2.
Operation 03
The chamfers 6 and 5 must be finished using two chamfering tools fixed in position 2 of the turret.
Operation 04
Finishing of chamfer 1 may also be performed simultaneously with operation 10 by providing a chamfering tool on the rear slide.
Operation 05
Semi-finish boring of hole 8 may be done using a carbide tool fixed in boring bar at position 3 of turret.
Operation 06
Hole 8 must be reamed and surfaces 2 and 3 be finish turned by a combination of tools fixed at position 4 of turret by using HSS reamer 18K6 and carbide tipped turning tool.