Hot Section Inspections (HSI's)
The hot section includes all components in the combustion and turbine sections of the engine. Scheduled inspections may involve visual inspection of hot section components, and limited dimensional checks and fits and clearances as called up in the maintenance schedule and described in the AMM. The term ‘hot section inspection' is usually interpreted to indicate a time related inspection of the hot section components. It may also be required following an over-temperature condition or hot start.
Some more in depth HSI's will require the removal of major components of the hot section. The modular construction of most modern gas turbine engine will enable this removal element of the task to be carried out on the wing, thus reducing the down time. To reduce this down time figure even more, some operators maintain a stock of ‘hot section' modules that are ready for immediate replacement, the removed item being returned for inspection to the operators overhaul facility.
Disassembly of Hot Section.
The disassembly/reassembly process must ensure that component parts are reassembled in the same position they came apart from. This will require marking of components. A note of caution here. When marking any hot section component do not use a marker that will leave a carbon deposit. Hot metal will absorb carbon which can lead to intergranular stress and failure of the component.
Line Inspection of Combustor Turbine Section.
On wing inspection of the combustor turbine section can be done visually through the jet pipe using a strong light source and a mirror and if required a magnifying glass. Boroscope inspection is also used as is, on occasion, non destructive methods of inspection such as dye-penetrant. As in other hot section inspections, the AME is most likely to see small cracks caused by compression and tension loads during heating and cooling. Other than on turbine blades and discs this type of distress is normally acceptable because after initial cracks relieve the stress, no elongation of crack normally occurs.
Erosion of blades and NGVs is also quite common, this brought about as a result of the wearing away of metal due to either the gas flow or impurities within the gas flow.
Combustion Section.
One of the most common faults found in the combustor section of a gas turbine engine is cracks. The combustion liner is made of a high temperature resistant steel that is subjected tom high concentrations of heat. The most common methods of checking for faults is by boroscope. With this tool the AME can easily view the internal combustion liner and fuel nozzles, and determine their airworthiness. During the inspection the AME is looking for signs of cracking, warping, burning, erosion and hot spots which may have developed possibly as a result of burner misalignment. What is observed is then compared with the manufacturers limitations.
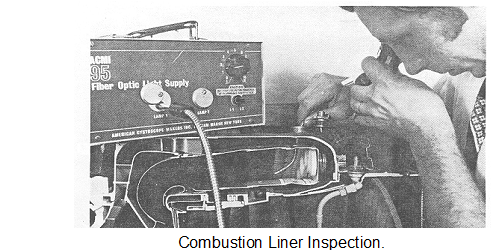
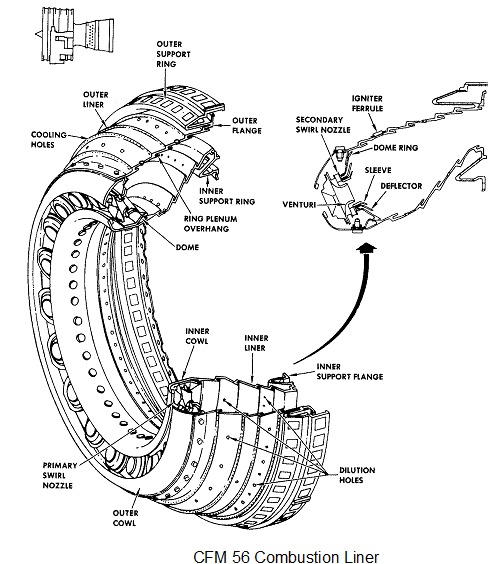