The Pure Planet Company† operates a recycling center that collects four types of plastic materials, then treats them so that they can be interfused-treating and interfusing are separate processes-into a salable product. Three different grades of this product can be made, depend-ing on the mix of the materials used (see Table 1 on the following page). Although there is some flexibility in the mix for each grade, quality standards specify the minimum or maximum amount of the materials allowed in that particular grade (expressed as a percentage of the total weight for that product grade). For example, one pound of Grade A product must contain no more than 4.8 ounces (30 percent) of Material 1 and at least 6.4 ounces (40 per-cent) of Material 2. Also note for each of the two higher grades, a fixed percentage is specified for one of the materials. These specifications are also given in Table 1, along with the cost of interfusion and the selling price for each grade.
The recycling center collects its plastic materials from some regular sources and, therefore, is normally able to maintain a steady rate for processing them. Table 2 gives the quantities that are available for collection each week (in tons), as well as the cost of treatment, for each type of material. The Pure Planet Company is solely owned by Green Earth, an organization that is devoted to dealing with environmental issues; Pure Planet's profits are all used to help support Green Earth's activities. Green Earth has raised contributions and grants, amounting to $50,000 per week, to be used exclusively to cover the entire treatment and interfusion costs for the plastic materials. The board of directors of Green Earth has also instructed the management of Pure Planet to divide this money among the materials in such a way that at least half of the amount available of each material is actually collected and processed.
Assignment1:
Using the information provided in Tables 1 and 2 as well as the additional restrictions speci-fied by Green Earth, management wants to allocate the plastic materials to product grades so as to maximize the total weekly profit (total sales revenue minus total treatment and interfusion costs).
1. Formulate the linear programming model for this problem,
2. Solve using EXCEL Solver and generate the answer and sensitivity reports, and
3. Present your solution in terms management can understand.
Additional Analysis (use the sensitivity report generated in Question 2 above to answer the following questions, do not re-solve the problem)
Management now wants to conduct some "what-if" analyses with your help. The product specifications are industry standards and cannot be modified. However, there is some uncer-tainty or flexibility with some of the other information. The answers to the following questions would help management better plan the processing of the recycled plastic material.
4. Pure Planet has excess capacity for treating and interfusing the materials. If they were to try to identify additional sources of materials (say, ¼ ton), for which of the materials should they try to do so? How would this affect the total profit?
5. The chemicals used for treating Material 4 are expected to increase in price, such that the treatment cost would go from $5.00 to $5.50 per pound. Inform management how this would change the solution and total profit.
6. Pure Planet would like to ask Green Earth for additional funding in order to process more of the recycled plastic materials, but would like to illustrate the benefit of doing so. How would the total profit change if the budget for treating and interfusing increased by ten percent (from $50,000 to $55,000)?
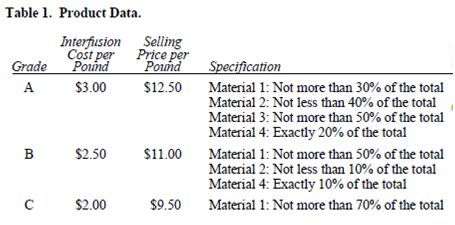
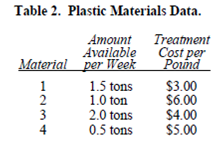