Q. Explain working of Digital Process Control?
Figure shows a block diagram for microcomputer-based control of a physical process, such as a chemical plant. A slight variation of the system can be used for automotive instrumentation in which sensors furnish various signals for speed, fuel reserve, battery voltage, oil pressure, engine temperature, and so on. The data are presented to the driver in one or more displays on the dashboard. In a physical process on the other hand, based on the display information, an operator can assess and direct the operation of the control process through a keyboard or other input devices to the microcomputer.
Various physical inputs, such as power and materials, are regulated by actuators, which are in turn controlled by the microcomputer. Electric signals related to the controlled-process parameters, such as pressure and temperature, are produced by various sensors, which in turn feed the information to the microcomputer. Actuators and sensors may be either analog or digital. Digital-to-analog (D/A) converters are used to convert the digital signals to analog form so as to suit the analog actuators, where as analog-to-digital (A/D) converters are employed to convert the analog sensor signals to digital form so as to suit the microcomputer.
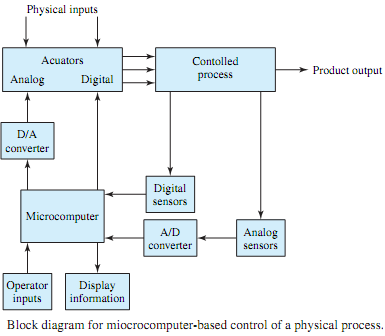
One can think of so many systems in daily practice controlled or monitored by microcomputers. Some examples include monitoring patients in intensive cardiac-care units of hospitals, nuclear-reactor controls, traffic signals, aircraft and automobile instrumentation, chemical plants, and various manufacturing processes.