Q. Explain Solid-State Control of DC Motors?
Dc motors, which are easily controllable, have historically dominated the adjustable-speed drive field. The torque-speed characteristics of a dc motor can be controlled by adjusting the armature voltage or the field current, or by inserting resistance into the armature circuit . Solid-state motor controls are designed to use each of these modes. The control resistors, in which much energy is wasted, are being eliminated through the development of power semiconductor devices and the evolution of flexible and efficient converters.
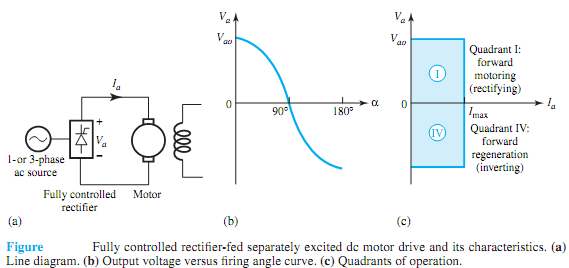
Thus, the inherently good controllability of a dc machine has been significantly increased in recent years by rectifier control, chopper control, and closed-loop control of dc motors. When a dc source of suitable and constant voltage is already available, designers can employ dc-to-dc converters or choppers. When only an ac source is available, phase-controlled rectifiers are used. When the steady-state accuracy requirement cannot be satisfied in an open loop configuration, the drive is operated as a closed-loop system. Closed-loop rectifier drives are more widely used than chopper drives. Only rectifier control of dc motors is considered here.
Controlled rectifier circuits are classified as fully controlled and half-controlled rectifiers, which are fed fromeither one-phase or three-phase supply. Figure shows a fully controlled, rectifier-fed, separately excited dc motor drive and its characteristics. A transformer might be required if the motor voltage rating is not compatible with the ac source voltage. To reduce ripple in themotor current, a filter inductor can be connected in series between the rectifier and themotor armature. The field can be supplied from the same ac source supplying the armature, through a transformer and a diode bridge or a controlled rectifier. While single-phase controlled rectifiers are used up to a rating of 10 kW, and in special cases even up to 50 kW, three-phase controlled rectifiers are used for higher ratings.