Dynamic balancing principles:
We must all be familiar with the effects of unbalance in one form or another, but perhaps the most common effect is that arising from wheel unbalance in motor cars. At resonance conditions it causes wobble or bounce, the effects of which are transmitted to the driver through the steering column. This effect may be so violent as to make the car unsafe or at least uncomfortable to ride in, and the continual vibratory movements set up, even outside the resonance range will increase the rate of wear on the various linkages and add to driver and passenger fatigue.
In order to increase passenger comfort, reduce wear and noise levels and also to increase the life of the engine between overhauls, design effort is put into the various aspects of minimising vibration in aero-engines. Design features are also included to permit correction of unbalance forces.
Efforts are made to design engine bearing housings and carcasses with suitable stiffness to avoid resonance in the engine running range. In addition, precise balancing instructions are issued to control the rotating forces on the bearings which could:-
a) be transmitted to other parts of the engine or airframe structure.
b) lead to engine failure in extreme cases.
The loads on the bearings are of three main forms. These are:
a) thrust loads due to the engine doing work.
b) journal loads due to the dead weight of engine parts.
c) unbalance loads.
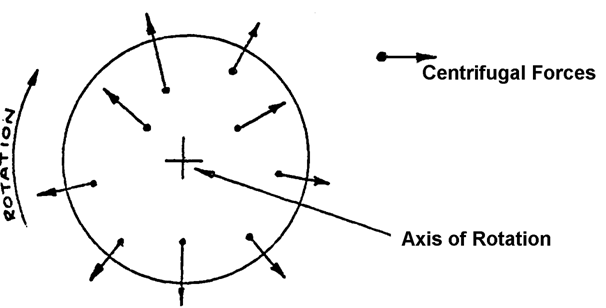
Centrifugal force acts on every particle which makes up the mass of the rotating element impelling each particle outwards and away from the axis, about which it is rotating, in a radial direction.
If the mass of the rotating element is EVENLY DISTRIBUTED about the axis of rotation, the part is BALANCED and rotates WITHOUT VIBRATION. However, if there is a greater mass on one side of the rotor than the other, the centrifugal force acting on this heavy side exceeds the centrifugal force on the light side and pulls the entire assembly in the direction of the heavy side.