Causes of unbalance
Unbalance may be caused by a variety of factors occurring singly or in combination with others. These factors include:-
a) Eccentricity
Eccentricity exists when the geometric centreline of a part or assembly does not coincide with its axis of rotation. This may be as a result of locating features (eg. spigot location, bolt holes, splines, serration's, couplings), being eccentric to the bearing location.
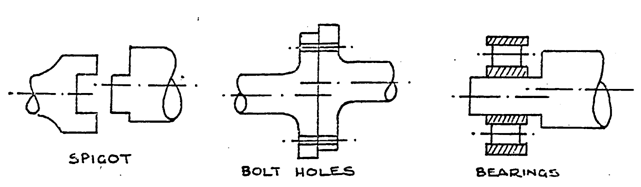
b) Variation in Wall Thickness
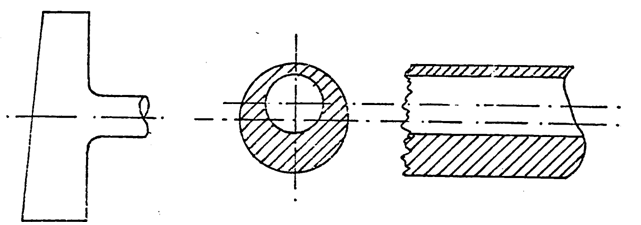
Variation in wall thickness may be as a result of eccentricity between an inner and outer diameter of a cylindrical type feature, or it may be as a result of a difference in thickness between a radial section of a disk type feature and the section diametrically opposite.
c) Blade Distribution
Unbalance can be caused by an unequal or unsymmetrical arrangement of a set of blades, either by reference to their mass moments or their dead weights depending on the size of the blades. This can be as a result of faulty weighting, inaccurate or illegible recording or assembly errors.
d) Unsymmetrical Features
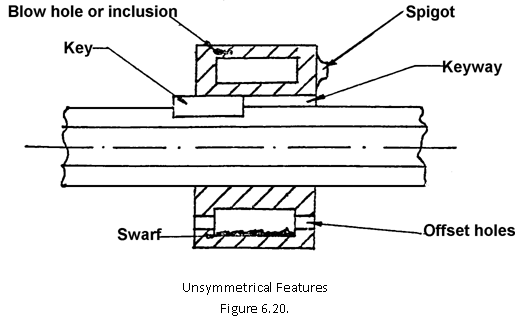
These may be due to manufacturing processes, such as blow holes in castings or design features such as offset holes, locating dogs, slots, keyways, etc.
e) Distortion
This can be caused by stress relieving, eg. after welding, or by unequal thermal growth during running.
f) Fits and Clearances
Clearance between mating parts allows relative movement of the parts and a consequent shift of the axis of rotation during running (or even during balancing). Joints incompletely assembled, eg. chamfers fouling radii, abutment faces not pulled together, may cause a ‘bent' rotor or an unsuitable joint, which may cause a shift during running. It is important to prevent separate locating, or fixing, features from influencing each other eg. bolt holes, spigot locations, serration's, etc. must be geometrically controlled to prevent ‘fighting' between more than one feature. See also the section on tooling, adapters, drives, dummy rotors, etc.
g) Swash
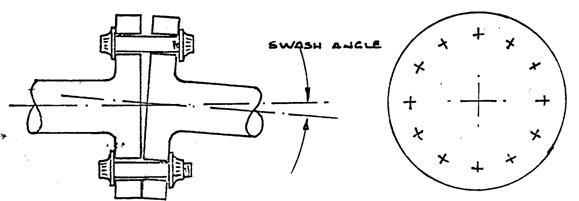
Swash is caused by out of squareness of abutment faces relative to the bearing diameter, abutment faces not being parallel across the component, eg. spacers, adjusting washers, disks, etc. It is important that the bolted joints are tightened in sequence and in increments according to the torquing instructions.
h) Miscellaneous
Foreign bodies inside assemblies, oil accumulation, carbon deposits, usually found when check balancing after running.