Aspects Of Scheduling
The difficulty is a modification of a flexible manufacturing cell at ABB's plant for the manufacturing of turbocharger in Baden, Switzerland. The difficulty is a little modified to make it more demanding via eliminating one lading station (or else the average use of the loading stations is below 40 percent for full use of all machines) and via changing the part mix to acquire an extra uniform distribution of the load in the system. Two various cases are considered. In the initial condition, the original loading times and continuous order release throughout the shifts are supposed. This concludes in moderate average queue lengths. In the second condition, the loading times are raised, various load levels for machines are generated, and the orders are released merely at the starting of each shift. These results in a considerably more tough decision problem at the loading station where currently long queues exists and the that termed as shading effect occurs.
The layout of the flexible manufacturing system is depicted in following figure. Within the underlying industrial system, there are five machines and two of them identical and two loading stations, a deburring station, and a washing station. Now, this is supposed that only one loading station is obtainable, or else utilization of the loading stations is restricted to only 40 percent. All parts have to be loaded initially after that one or two machining operations obey, and after that deburring, reloading, washing, another one or two machining operations, deburring, unloading and washing.
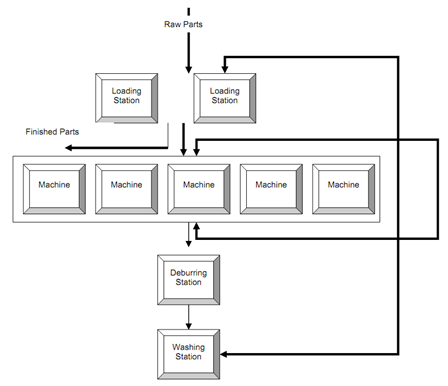
Figure: Layout of FMS
There are 11 elements types. The greatest number of operations per element type is 11, the smallest is nine. Flow diagram of all 11 elements types are represented in following figure. The operation times for machining operations are specified in Table no.1. Operation times at the stations WASH, LOAD, DEBUR are equal for all the parts. During case 1, the operation times are as:
Initial loading
|
8 min
|
Unload/reload
|
13 min
|
Final unloading
|
5 min
|
Deburring (each time)
|
8 min
|
Washing (each time)
|
6 min
|
During case 2, all the operation times on the loading stations are raised via five minutes; the other operation times keep not changed. This generates a bottleneck on the loading station through that all elements should pass three times, and thus a more demanding decision difficulty at the loading stations results.
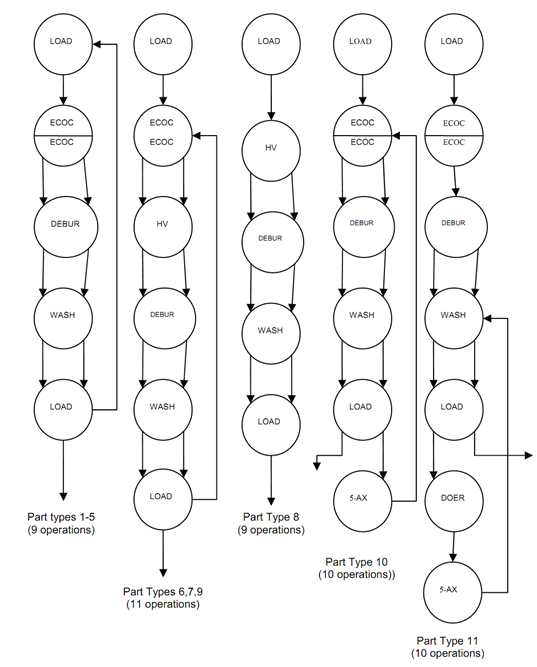
Figure: Machining Sequences for Part Types
Table no.1: Machining Times for Part Types
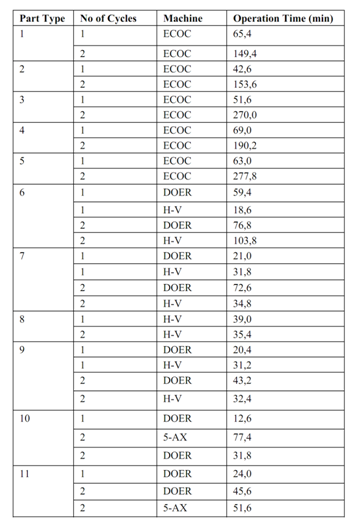