Reference no: EM131452165
Assignment
1. The Bloomington Bike Company produces two models: the Basic and the Supra. Herb Hoosier, the owner, plans to assemble 15 Basics and 10 Suprasin each week during periods 4 to 8. Product structure trees for each bike are shown below:
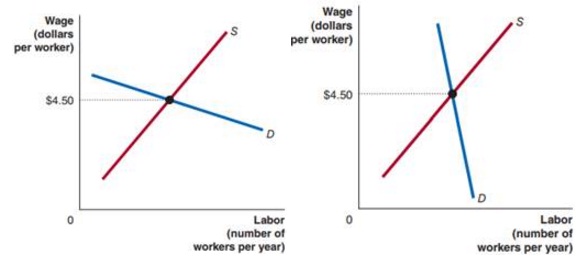
Develop a materials requirement plan (MRP) for component parts K and W over the next eight weeks. Data on all lead times, current inventory and ordering rules are given below: Scheduled receipts are: Period 1: 20 B's, 18 W's; Period 2: 20 S's, 15 F's. A sample MRP table is provide below.
ITEM
|
LEADTIME (WKS)
|
ON HAND
|
LOT-SIZING RULE
|
B
|
2
|
5
|
Lot-for-lot
|
S
|
2
|
2
|
Lot-for-lot
|
X
|
1
|
5
|
Multiples of25
|
W
|
2
|
2
|
Multiples of 12
|
F
|
1
|
10
|
Multiples of 30
|
K
|
1
|
3
|
Lot-for-lot
|
Q
|
1
|
15
|
Multiples of 30
|
M
|
1
|
0
|
Lot-for-lot
|
|
1
|
2
|
3
|
4
|
5
|
6
|
7
|
8
|
Gross requirements
|
|
|
|
|
|
|
|
|
Schedule receipts
|
|
|
|
|
|
|
|
|
Projected on hand
|
|
|
|
|
|
|
|
|
Net requirements
|
|
|
|
|
|
|
|
|
Planned order receipt
|
|
|
|
|
|
|
|
|
Planned order release
|
|
|
|
|
|
|
|
|
1. A ?rm makes car seats for an automaker in two varieties: leather and fabric. The standard labor-hours for these are 1.2 and 1.0 hours, respectively. The seats are made in two work centers, sewing and assembly, where the average percentage of work has been 55 percent for sewing and 45 percent for assembly. The following schedule for the next six weeks is given.
Week
|
1
|
2
|
3
|
4
|
5
|
6
|
Leather
|
15
|
20
|
18
|
21
|
15
|
13
|
Fabric
|
65
|
60
|
62
|
59
|
65
|
67
|
a) Using the CPOF (Capacity Planning Using Overall Factors) approach, calculate the labor-hours needed in each of the two work centers in each week.
b) Suppose the following information is given. Using the capacity bills approach, calculate the labor-hours needed in each of the two work centers in each week.
Work Center
|
Time (hours/unit)
|
Leather
|
Fabric
|
Sewing
|
0.7
|
0.6
|
Assembly
|
0.5
|
0.4
|
Total
|
1.2
|
1.0
|
2. A manufacturing facilityproduces two types of a product: Standard and Deluxe. The process flow for both types of production is shown in the following chart. Both types are first processed through steps A1 and A2.
The Standard then goes through steps A3 and A4 while the Deluxe is processed through steps A5, A6, and A7. Both types finish at A8. The numbers in parentheses indicate the minutes it takes for that activity to process a singleunit.

a) Which step is the bottleneck for the Standard products? Which step is the bottleneck for the Deluxeproducts?
b) What is the capacity (measured as units per hour) of the facility to process the Standard products? What is the capacity to process the Deluxeproducts?
c) If 60 percent of the products are Standard and 40 percent are Deluxe, what is the average capacity (measured as units per hour) of the facility?
d) Following Part c), if the actual throughput is 3.2 units per hour, what is the utilization of each step (A1-A8)?