Reference no: EM131467079
Project Objective
This project is concerned with the modeling, design and implementation of control strategies for the water twin tank process. The controlled variable is the water level in tank 2. The manipulated variable is the pump power, on the water inlet flow line to tank 1. Water flows from tank 1 to tank 2 and from tank 2 to the reservoir because of hydraulic pressure difference. Detailed, first principles-based, dynamic models as well as empirical models for the two water levels as a function of the manipulated variable must be developed and used for controller design. The PAS TuneWizard must be used to develop empirical models and tune the tank 2 water level controller.
Project Deliverables
You are being asked to prepare a written report on the design and performance of your control strategies. Your report must follow the rubric for technical reports discussed at the beginning of the course. Among others, it must contain the following key pieces of information:
Analytical Modeling (open loop)
1. First principles based dynamic models for the water levels (tank 1 and tank 2) with pump voltage as the input variable
2. Linearization of any non-linear models and development of transfer functions between:
a. tank 1 level and pump voltage.
b. tank 2 level and tank 1 level.
c. tank 2 level and pump voltage.
Empirical Modeling (open loop)
Development of transfer function model between:
a) tank 1 level and pump voltage.
b) tank 2 level and tank 1 level.
c) tank 2 level and pump voltage.
Comparison of transfer functions obtained using analytical and empirical methods
Single Feedback Control Structure
- Design of a PID controller when the controlled variable is the tank 2 level and manipulated variable is the pump voltage.
o Tune the level controller using your preferred tuning method and/or anyone of the methods in the PAS software. Two sets of tuning parameters for the tank 2 water level control loop will be developed: one using the analytical model and another using the empirical model.
- Evaluation of the closed loop performance on the experimental process for setpoint changes of
+1.5 inches in tank 2 level.
o Two sets of closed loop performance will be generated using each of the tuning parameters obtained in the previous step.
o Manual tuning adjustments may be required for improved setpoint control
Cascade Control Structure
- Design of a cascade control structure involving two controllers of PID form to control tank 2 level. In this cascade structure, the secondary controller will control tank 1 level by adjusting the pump voltage while the master controller will control tank 2 level by adjusting the setpoint of tank 1 level controller.
- Tune the level controllers using your preferred tuning method and/or anyone of the methods in the PAS software.
- Evaluate the closed loop performance on the experimental process for setpoint changes of +1.5 inches in tank 2 level.
o Two sets of closed loop performance will be generated using each of the tuning parameters obtained in the previous step.
o Manual tuning adjustments may be required for improved setpoint control
Hints:
- A similar problem (for one tank only) was discussed in class and is described in the class textbook.
- Think how the hydraulic pressure difference will affect the flow from tank 1 to tank 2. Does it depend on tank 1 level, tank 2 level or both?
- You may need to develop a relationship between the pump voltage and the resulting flow rate into tank 1. Think creatively on how to develop this relationship. A similar problem was solved in ENGR 3410!
- To develop the analytical models, an initial steady state must be established. Try a pump voltage value in the range of 3 to 3.25 VDC.
Notes:
- You will work in teams to complete this project. However, each team member will prepare his/her own report.
- The rubric for Technical reports must be followed
- If closed loop performance evaluation is not experimentally done, then your FINAL PROJECT grade is automatically zero.OPERATING
INSTRUCTIONS FOR TWIN WATER TANK EXPERIMENT
I. Project Description
- For easy understanding and use, the experimental process is being divided in three sections/components:
1. Process: twin-tank setup, a reservoir, 2 ultrasonic level transducers, ball valves, and a DC pump.
2. Data Acquisition Station: hardware that carries out the input-output (I/O) operations and allows communication between the Process and the Operator Station.
3. Operator Station: a PC based system with an appropriate Human-Interface-Machine (HMI) to operate and control the Process.
A. Process
- The physical layout of the process is designed as an interacting system of two tanks in series. The two identical tanks are made out of acrylic containers They are coupled by an ordinary poly vinyl chloride (PVC) ball valve type and PVC conjunction pipe, of which the diameter (d) is 0.5 inches. A simple process schematic is shown in Figure 1.
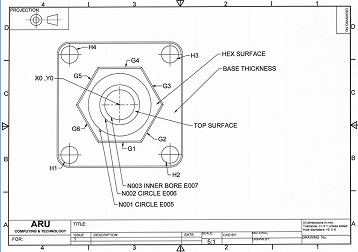
Fig 1 Interacting Series Tanks
Physical dimensions of the twin-tank process:
Dimensions of Tank 1 and Tank2
Approximately similar dimensions
5½ in x 5 in x 14½ in (L x W x H)
13.97 cm x 12.7 cm x 36.83 cm (L x W x H)
Dimensions of Reservoir
14 in x 23½ in x 13½ in (L x W x H)
35.56 m x 59.69 cm x 34.29 cm (L x W x H)
- The liquid levels in both tanks are regulated by the volumetric flow rate into the tank 1, which is affected by the voltage to the water pump (13.5 V - 1.8 A). Both tank level controllers (depends on single loop or cascade control), programed in the LabVIEW platform, manipulate a pulse width modulation (PWM) signal through the NI USB6009, a National Instrument data acquisition device (DAQ), to control the water pump voltage.
- Liquid levels are measured and calibrated by two ultrasonic level measurement transducers or sensors in inches. Signals, sending from the level sensors, typically 4
- 20 mA, are transmitted to the input signal channels, AI1 and AI2, of the DAQ NI USB 6009.