Reference no: EM132298707
Advanced Rock Breakage Assignment -
Question 1 - Design a surface blast for the following conditions:
a) Ore of density 2.9 tonnes/m3.
b) Grade control blast, also known as a paddock blast.
c) Tonnage to be blasted 580,000 tonnes.
d) Bench height 10m.
e) Blasted width 75m.
f) Assume dry and reactive rock conditions.
g) Conductive ore so Nonel initiation to be used.
As part of the design students are to select an appropriate blast hole diameter and drill rig, design the blast, select appropriate explosives, primers and initiation pattern. Students also need to consider hole loading.
Question 2 - Design a coal overburden throw/cast blast for the following situation:
a) Blast length 1000 m.
b) Blasted bench width 70 m.
c) Bench height 25 m.
d) Overburden of shale/siltstone/sandy shale, average density 2.7 tonnes/m3.
e) Wet conditions.
f) Hole diameter 250 mm.
Design the blast pattern, select explosives, primers and initiation system, detail initiation sequence.
Question 3 - A surface mine blasting operation has been designed utilising 200 mm diameter holes to blast sandstone with 12m long holes, using an explosive with a powder factor of 0.5 kg/m3 and a density of 1100 kg/m3. The blast is 100 m long along the bench and the bench width is 30 m. For sandstone assume k = 23. Determine the maximum throw length for both bench face and cratering fly rock and provide a sketch detailing maximum throw length and the clearance distances for equipment and personnel for this blast. Note you will need to determine burden and spacing assume B = S, you will also need to determine the stemming length.
Question 4 - Design a drilling hole and blast design pattern for the following input conditions:
- Blasthole diameter: 63 mm.
- Empty blasthole diameter: 150mm (2 empty blastholes to be used in the cut).
- Tunnel width: 6m.
- Tunnel height: 5.5m Smooth blasting in the roof.
- Lookout for contour holes γ= 3o or 0.05 rad Angular deviation α2 = 0.001m/m.
- Collar deviation α1 = 0.02m.
- Explosive: potentially wet conditions thus a pumped emulsion is to be used
- Density = 1100 kg/m3.
- Rock constant c = 0.45.
Please list any further assumptions.
Question 5 - Students are to discuss methods available for developing draw cones in block/panel caving.
Question 6 - When blasting sulphide ores the potential for sulphide dust explosions exists. What is a sulphide dust explosion? What should be included in a sulphide dust explosion management plan? How can the effects of sulphide dust explosions be mitigated? What industry codes of practice exist regarding sulphide dust explosions?
Question 7 - A particular mine site is proposing to use 150 mm diameter holes and 15m benches using pored ANFO as their explosive of density 800 kg/m3. Site measurements have yielded the following in terms of blast vibration, site law exponent = -1.5 and site law constant = 1500. The benches are proposed to be blasted in 100m long sections with a bench width of 25 m. S = 1.15 x B and the benches are blasted in an open chevron pattern.
a) Design a bench blast pattern.
b) Determine the ground vibration at a distance 500m from the blast.
c) If the maximum ground vibration 25m from the blast is set at 40mm/s what changes would you need to make to your design?
Project -
Part 1 - Design a surface blast for the following conditions:
h) Ore of density 2.7 tonnes/m3, granite.
i) Bench height 10m.
j) Blasted length 200m.
k) Blasted width 100m.
l) Assume dry rock conditions.
m) Conductive ore so Nonel initiation to be used.
As part of the design, students are to select an appropriate blasthole diameter and drill rig, design the blast, priming and initiation pattern. Students also need to consider blasthole loading and priming.
Students also need to define the dimensions of the exclusion/safe zones for both personnel and equipment from front of face and cratering flyrock.
Part 2 -
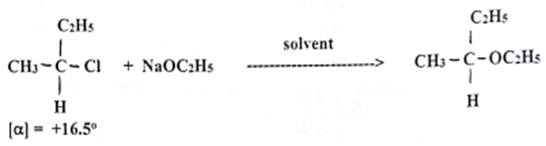
The orebody grade is 2.9% Cu with a cut-off grade of 0.7%. Walls are determined by this cut-off grade. Footwall dilution generally grades 0.2% and hangingwall 0.5%. During normal operation, average dilution is 1m from each wall.
The blasthole toe spacing is generally 3m and burden 3.6m. Holes are charged with 150mm long primers weighing 1kg and are pressure charged with ANFO to an average 1m from the collar, length of charge varying in each collar area.
1. Lay out a ring and show a charging pattern.
2. Calculate the powder factor for this pattern.
3. What will be the tonnage/ring and diluted grade?
4. The mine can handle grades as low as 2% whilst still maintaining an adequate profit. If grade is maintained in the hanging wall how far can we mine before grade is diluted to 2%?
5. Comment on whether the company should or should not mine this hangingwall material.
6. If the cost of primers is $4 each, detonators $4.50 each and ANFO costs $3/kg determine the cost per tonne during normal mining?
7. If the stope is 30m in length and swell factor is 30% what is the minimum number of rings that can be blasted prior to mass blasting of the stope?