MRP System Inputs
Inputs of an MRP system include master production schedule, bills of material, and inventory records file.
Master production schedule
The Master Production Schedule (MPS) file contains information about when and how many units of finished products are required. It also contains information about the available cumulative lead-time for purchasing, receiving, fabricating, and assembling. This information is derived from an aggregate production plan and is based on demand forecasts. Based on this information from MPS, MRP system generates a replenishment plan for items needed in the production of the final product.
The time horizon in the MPS is divided into time buckets. Managers can use shorter time buckets such as a day or two to plan short-term requirements, and longer time buckets such as a fortnight or a month to plan long-term requirements. However, the most frequently set period for practical purpose is about a week. MRP system based planning is based on the assumption that production capacity is sufficient to produce everything on or before the pre-designated dates given in the MPS. To make the schedule feasible, operations managers run the MRP program repeatedly, each time making some changes in the master production schedule, lead times, or material requirements, until the schedule attains feasibility. MPS is described in Chapter 10.
Bills of material
The Bills of Material (BOM) contain the list of materials along with the quantity required to produce one unit of a product. The BOM file shows the hierarchical levels or phases a product goes through during production (from raw material stage to end product). It consists of the complete list of all end products, the structure (subassemblies, parts, and raw materials which constitute the product assembly) of the products, and the quantity of each item required for producing each higher-level item in the product hierarchy. It also contains information about whether a particular item was produced internally or purchased from external sources. The purchase or production lead-time to acquire the item is also mentioned. The file is also referred as the product structure file or indented parts list. Figure 13.3 presents a product structure chart for a hypothetical product. In this chart, one unit of a finished product, its eight different component (P1 to P8) and different phases or level of production are shown.
In the Figure 13.3, the hypothetical end product is assembled from two component parts, P1 and P2. The number "3" next to part P4 indicates that three units of P4 are required to make a unit of P1. In the hierarchy, the component parts at the lower levels are combined to form the inventory item at the next higher level. For instance, two units of the part P7 and one-unit of part P8 are processed to make one unit of part P4. It can be seen that the part P4 is used in more than one level of production. This situation causes some inefficiency in computer processing because MRP program has to consider more than one level where the part is required while processing material requirements. To overcome this problem, managers generally restructure the BOM, so that a common component appears at the same level throughout. This restructuring is called low-level coding as the common component is incorporated at the lowest level at which it appears in the original product structure chart. It is important for the operation managers to revise the BOM file at regular intervals and update it accordingly.
Figure : Product Structure Chart
Problem
Based on the bills of material shown in Figure, identify purchase quantities of G, F, J items to produce 10 units of A.
Solution
From Figure, we can identify the number of lower level components required to produce components at the next higher level.
The lowest level components in the Figure are F and G. G is required to manufacture E and I. Two units of G are needed to manufacture one unit of E and three units of G are required to manufacture one unit of I. One unit of E is required to produce one unit of B and three units of B are required to produce one unit of A. 2 units of I are required to produce 1 unit of C and 1 unit of C is needed to produce 1 unit of A. Therefore, one unit of A requires three units of B, one unit of C and two units of D. Similarly, one unit of B requires one unit of E and three units of F. One unit of C requires four units of H and two units of I. One unit of D requires one unit of J and four units of F.
Therefore, the total quantity of G that must be purchased is = (2×1×3×10) + (3×2×1×10) = 60 + 60 = 120
Similarly,
Total quantity of F that must be purchased is = (3×3×10) + (1×2×1×10) + (4×2×10)
= 90 + 20 + 80 = 190
Total quantity of J that must be purchased is = (1×2×10) = 20
Total quantity of H that must be purchased is = (1×4×10) = 40
Figure : Bill of Material for Product A
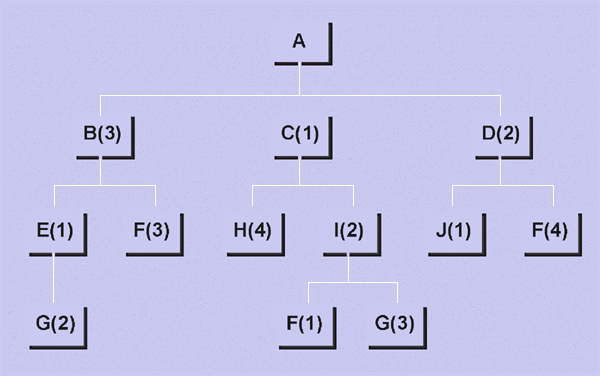
Problem
Given the product structure tree shown in Figure 13.4, how many units of F overall are required to manufacture 200 units of A? The on-hand inventory available is 100 units of subassembly D and 100 units of subassembly B.
Solution
Quantity of A to be produced = 200 units
Quantity of D required to produce 200 units of A = 400 units
Available inventory of D = 100 units.
Quantity of D to be produced = 300 units
4 units of F are required to produce one unit of D. Hence, 1200 units are required to produce 300 units of D.
Quantity of B required to produce 200 units of A = 600 units
Available inventory for B = 100 units
Quantity of B to be produced = 500 units
3 units of F are required to produce one unit of B. Hence, 1500 units are required to produce 500 units of B.
For every unit of A, one unit of C is required and for every unit of C, two units of F are required. Hence, for 200 units of C, 400 units of F are required.
The total quantity of F required to produce 200 units of A = 1200 + 1500 + 400 = 3100 units.
Inventory records file
In a typical production organization that uses MRP, many items (often ranging in thousands) are purchased, withdrawn from stock, moved to other departments or distribution outlets, processed, and assembled. Sometimes, these items do not reach their intended locations in time or items received are defective or rejected. All these issues complicate the task of inventory management and necessitate an effective filing system for all inventory transactions. The inventory records file is a computerized file with a complete record of each material held in the inventory. It contains all the information about inventory levels - levels at the beginning of the planning horizon and the details of the expected arrivals of inventory during that period. It also contains information about vendors like their names and addresses, and the time required for supplying materials, parts, etc. Organizations hold some components and parts as end products that are supplied to customers as replacement parts or spare parts. These parts are not included in the MPS, as they have no role in the production process. They are recorded directly into the inventory records file, and become a part of the MRP system. Though accuracy is important for all the elements of the MRP system, it is most crucial for the inventory records file. For instance, if an organization, by mistake, does not record the removal of an item from stock, it may later schedule considering the out-of-stock components. This would lead to inconsistencies in the future schedules.
Email based Operations Management assignment help - homework help at Expertsmind
Are you searching Operations Management expert for help with MRP System Inputs questions? MRP System Inputs topic is not easier to learn without external help? We at www.expertsmind.com offer finest service of Operations Management assignment help and Operations Management homework help. Live tutors are available for 24x7 hours helping students in their MRP System Inputs related problems. We provide step by step MRP System Inputs question's answers with 100% plagiarism free content. We prepare quality content and notes for MRP System Inputs topic under Operations Management theory and study material. These are avail for subscribed users and they can get advantages anytime.
Why Expertsmind for assignment help
- Higher degree holder and experienced experts network
- Punctuality and responsibility of work
- Quality solution with 100% plagiarism free answers
- Time on Delivery
- Privacy of information and details
- Excellence in solving Operations Management questions in excels and word format.
- Best tutoring assistance 24x7 hours