Developing a Product Layout
The design for developing a product layout is partly established when each part of the product is designed and the different steps required to make it are determined. The volume of production will determine the most economical process, and the process technology will determine the sequence of steps which have to be performed in production. Finally, the equipment and workstations are placed along a line in that sequence. Figure 6.4 shows some of the possible line arrangements.
There might be many possible sequences to arrange workstations and equipment for the same product. Line-balancing, a mathematical model, is used for determining appropriate ways to group the tasks to be performed at each workstation.
Line Balancing
Line balancing is a part of the assembly line study that comprises the selection of the appropriate combination of work tasks to be performed at each workstation so that the work is performed in a feasible sequence. The line balancing mainly ensures that each workstation gets equal amount of the time approximately.
Line balancing is achieved by breaking the total amount of work to be performed on a line into tasks. These tasks are assigned to workstations that allow the work to be performed in a feasible sequence within an acceptable cycle time. The time between completion of successive items on the line is termed as cycle time. The cycle time is determined by the maximum time required at any workstation. Work on the line cannot flow faster than it can pass through the slowest-stage, which is referred to as bottleneck. To avoid the bottleneck, some of the work tasks from workstations that deal with more work are assigned to workstations with less work.
Steps in assembly line balancing
The following steps are needed to balance an assembly line:
I. The sequential relationship among different tasks is specified by using a precedence diagram.
- The cycle time is determined by using the following formula:
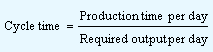
Figure: Some Possible Line Arrangements
II. The theoretical minimum number of workstations required to satisfy the cycle time is determined using the following formula:
Nt = T/C
Where Nt = Theoretical number of workstations
T = Sum of task times
C = Cycle time
III. A set of rules is identified to shortlist and select the tasks to be assigned to workstations. A sample set of rules is given below.
a) Identification of feasible (remaining) tasks for the same station:
From the unassigned tasks, identify the task(s) which can be assigned next to the same station, subject to two constraints:
-
The precedence rules should not be violated.
-
The individual time required for each of these feasible (remaining) tasks should be less than the unassigned time for the station, whereUnassigned time for a station = Cycle time - (Sum of the time required for all previous tasks that have been assigned to the station)
Note:
-
When there is no feasible (remaining) task for the same station, move on to the next station.
-
When there is exactly one feasible remaining task for the same station, assign it as the next task for the same station.
-
When there are multiple feasible remaining tasks for the same station, use the following tiebreaker rules to shortlist/select the next task for the same station.
b) Shortlist the tasks with most followers, among the feasible (remaining) tasks for the same station:
From the feasible (remaining) tasks for the same station, shortlist the task(s) which has (have) the most followers.
c) Select the task with the longest operation time: From the shortlisted tasks with most followers, select the task which has the longest operation time, and assign it as the next task for the same station. Sometimes, there may be many such tasks. In this case, one of these tasks with the longest operation time can be (arbitrarily) assigned as the next task for the same station.
IV. This set of rules is applied iteratively till all the tasks are assigned. At the end of this process, the actual number of work stations (Na) required may be greater than or equal to the theoretical number of work stations (Nt).
The efficiency of the balance is calculated by using the following formula.
Efficiency = T/Na * C
Where, T = Sum of task times
Na = Actual number of workstations
C = Cycle time
V. The balance is accepted if the efficiency is satisfactory, otherwise balancing is done using a different decision rule.
Mixed-model Line Balancing
So far we assumed that only one product was produced in each assembly line. But, to meet the demand for a variety of products many manufacturers consider mixed-model line balancing. Mixed model lines involve multiple lot sizes, lot sequencing, different setup times for each lot, differing workstation sizes along the line, and task variations that make it very difficult to design. As such, no technique exists to provide the optimum assignment of tasks to workstations in mixed-model lines.
The objectives of a mixed-model line design are to minimize idle time and minimize the inefficiencies caused by changing from model to model. Though many techniques such as integer programming, branch and band techniques, and simulation are used by researchers, they are unable to find the optimal solution for a realistic sized, real-world problem.
Email based Operations Management assignment help - homework help at Expertsmind
Are you searching Operations Management expert for help with Developing a Product Layout questions? Developing a Product Layout topic is not easier to learn without external help? We at www.expertsmind.com offer finest service of Operations Management assignment help and Operations Management homework help. Live tutors are available for 24x7 hours helping students in their Developing a Product Layout related problems. We provide step by step Developing a Product Layout question's answers with 100% plagiarism free content. We prepare quality content and notes for Developing a Product Layout topic under Operations Management theory and study material. These are avail for subscribed users and they can get advantages anytime.
Why Expertsmind for assignment help
- Higher degree holder and experienced experts network
- Punctuality and responsibility of work
- Quality solution with 100% plagiarism free answers
- Time on Delivery
- Privacy of information and details
- Excellence in solving Operations Management questions in excels and word format.
- Best tutoring assistance 24x7 hours