Trend Monitoring
It is continuous or regular measurement and recording of data, collected during operation, to indicate variations in the conditions of the machine or its components, in the interests of safe & economical operation. This needs thorough knowledge in the selection of suitable and measurable parameters to indicate the deterioration of machine or component. The trend in this measurement that could happen with running time when deterioration exceeds a critical stage and the way in which such trend monitoring can give a lead time before the deterioration reaches a shutdown level are interpreted in Figure
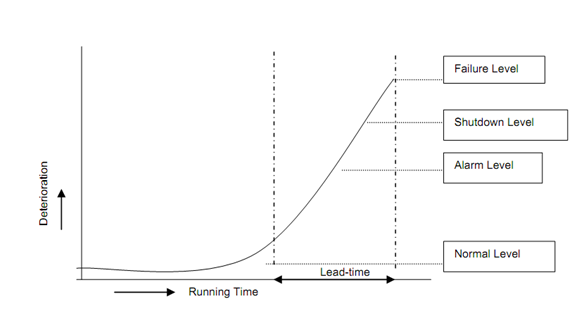
Figure: Trend Monitoring
Various states the equipment expected to undergo before breaking down are shown in the above Figure 1.
Normal Level
It is the state of the equipment in which it is running satisfactorily and production is within the normal range.
Alarm Level
It is the state developed in the equipment due to early stage of occurrence of the failure/fault and is noticed by some predetermined symptoms of the failure. For example, we may most likely get sneeze or cough or head-ache, etc. before getting fever. Low production, lower quality of the output, heavy noise, vibrations, bad-smell, discoloration, etc. are some of the symptoms for noticing the alarm level of the failure or fault of the equipment.
Shutdown Level
If neglected even after reaching the alarm level, the fault grows and reaches a state at which the equipment will not co-operate or a considerable loss of output is observed. This state is called shutdown level. This state is at threshold of the breakdown level. The equipment should necessarily be closed or shutdown and should not be run any longer in the interest of preventing the failure.
Breakdown Level
This is the ultimate and final failure state of the equipment at which stoppage of production or catastrophe even with a possible damage can occur.
Lead Time
It is the duration between the points of start of failure to breakdown in process of deterioration of the equipment. In other words, it is time gap between last point of the normal level and breakdown level of the equipment. The lead-time is one of the main merits of using trend monitoring rather than the simple alarms of automatic shutdown devices used in permanent monitoring.
In most cases both methods, condition checking and trend monitoring, are used together. With the use of sensors, automation of monitoring is possible. A permanent monitoring by such sensors can prevent catastrophic failures by alarming or stopping the machine automatically when the parameter (selected to indicate the machine condition) exceeds a predetermined level. Of course, the pre- selected warning/alarm levels, based on the experience of the users show a way to optimize the life of wearing machine parts. Thus in condition monitoring, the repairs are carried out only when the machine condition deteriorates to predetermined level. In other words, the repairs or replacement of parts take place only when it has definitely been proved that a fault exists and left as 'not-repaired' would result in unsatisfactory operation such as decrease of production or catastrophic breakdown with possible damage to other machine parts and disruption of production.