PROPELLER CONSTRUCTION
METAL PROPELLERS
Most metal propellers have forged alloy blades protected from corrosion by anodising and often further protected by polyurethane enamel. A few propellers with hollow steel blades are still flying, but these are usually found only on special-purpose aeroplanes.
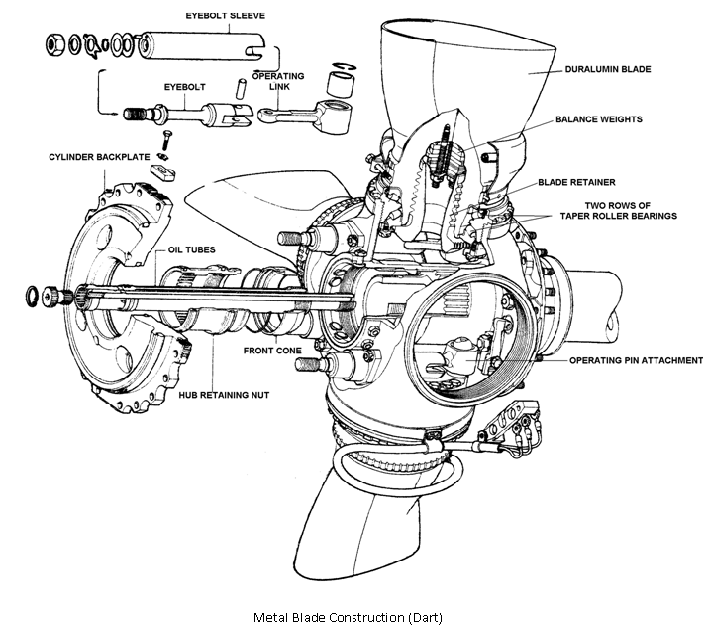
Laminated wood, forged aluminium alloy, and brazed sheet steel propellers have been the standard for decades. But the powerful turbo-propeller engines and the demands for higher-speed flight and quieter operation have caused propeller manufacturers to exploit the advantages of modern advanced composite materials.
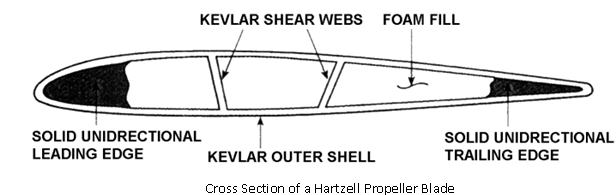
Composite material used in propeller manufacturing consist of two constituents; the fibres and the matrix. The fibres most generally used are glass, graphite, and aramid (KevlarTM), and the matrix is a thermosetting resin such as epoxy.
The strength and stiffness of the blades are determined by the material, diameter, and orientation of the fibres. The matrix material supports the fibres, holds them in place, and completely encapsulates them to protect them from the environment.
Because the fibres have strength only parallel to their length, they are laid up in such a way that they are placed under tensile loads.
The typical Hartzell composite propeller, like that in Figs.2.2. to2.4. below, has a machined aluminium alloy shank, and moulded into this shank is a low-density foam core. Slots are cut into the foam core and unidirectional Kelvar shear webs are inserted. The leading and trailing edges are made of solid sections of unidirectional Kelvar, and laminations of prepreg material are cut and laid up over the core foundation to provide the correct blade thickness, airfoil shape, pitch distribution, planform, and ply orientation. The outer shell is held in place on the aluminium alloy shank by Kelvar filaments impregnated with epoxy resin wound around the portion of the shell that grips the shank.
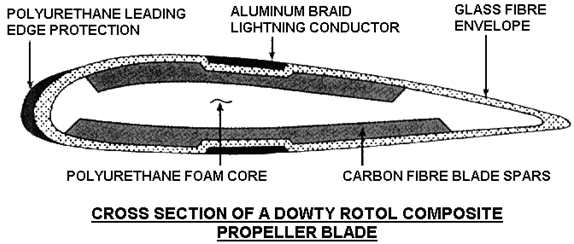
Some Hartzell blades have a stainless steel mesh under the final layer of Kevlar to protect against abrasion, and a nickel leading edge erosion shield is bonded in place.The spar is machined to its correct configuration and placed in a mould cavity, and the core foam is injected around it. The foam is cured and is removed from the mould. Glass fibre cloth, with the correct number of plies and the proper ply orientation, is then laid up over the cured core. The complete lay-up is then placed in a second mould that has the shape of the finished blade. The resin matrix is injected to impregnate all the fibres, and is cured with heat and pressure.
The Dowty Rotol composite propeller blade has two carbon fibre spars that run the length of the blade on both the face and back and come smoothly together at the blade root. The carbon fibres and pre-impregnated glass fibre cloth are laid up with the proper number of plies and in the correct ply orientation and are placed in a mould. Polyurethane foam is injected into the inside of the blade, and the entire unit is cured under head and pressure.
The Dowty Rotor blade is secured in the hub by expanding the carbon fibres spars with tapered glass fibre wedges and locking them between the inner and outer sleeves.
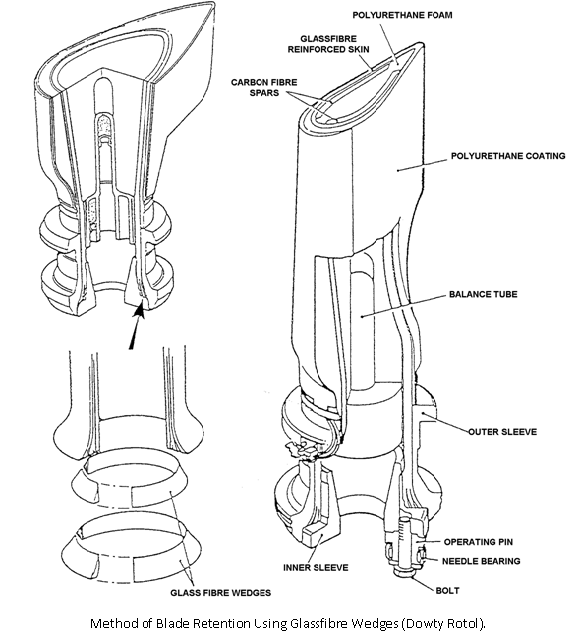
Composite propeller blades are much lighter than metal blades capable of absorbing the same amount of power. The lighter blades impose less centrifugal loading on the hub, allowing it to be made lighter. Composite blades have very low notch sensitivity, and their foam cores absorb much of the vibration that would damage metal propellers. While composite blades currently cost more than metal blades, their greater efficiency and longer life make them much more cost effective.